Au SAE-J1939 Simulators Ver 1.00A are well designed devices capable of simulating majority of SAE-J1939 signal on a vehicle network. A typical SAE J1939-15 network topology is illustrated in Figure 1.
6 editions of SAE-J1939 simulator Ver 1.00A are provided by Au Group Electronics to meet various users' needs:
This document will introduce major hardware features, important parameters, operating instruction, and data configuration for all 6 editions of Au SAE-J1939 Simulators.
Au SAE J1939 Simulator Engine Basic Edition(s) support majority of SAE J1939 engine parameters:
OPERATING INSTRUCTIONS:
All 6 editions of Au SAE J1939 Simulators can be operated by just controlling 3 push buttons. It generates SAE J1939 signal for product developers, testers, operators and manufacturers.
POWER ON:
-
Connect +10 ~ +32V DC to the "+12V power" and "ground" pin on the DB9 male connector, connect CAN_H and CAN_L to the CAN network (figure 2b)
-
The POWER LED lights up.
-
The simulator resumes the last saved operating mode (static mode or dynamic mode).
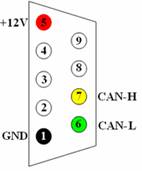
Figure 2b DB9 BUS Male Connector
OPERATING MODE (STATIC/DYNAMIC):
After power on, and connect CAN_H, CAN_L to a J1939 network (figure 2b), the Au SAE J1939 Simulator will work on either static mode or dynamic mode.
-
Static mode: generate steady SAE J1939 signal, two push buttons (UP and DOWN) is used to change the data outputs
-
Dynamic mode: All data automatically change in SAE J1939 defined range without human interfering
-
Press and hold both MENU+UP button for more than 1 seconds to switch between dynamic mode and static mode
PUSH BUTTON FUNCTIONS AND LED STATUS:
Au SAE-J1939 Simulator equipped with 3 push buttons (MENU, DOWN, UP) and 9 LEDs. The position of push buttons, LEDs, BUS interface, RS232 interface, is illustrated in figure 3. Each LED is named after its function.
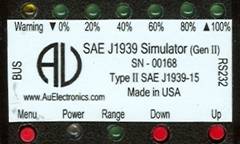
Figure 3 – Position of push buttons, LEDs, RS232 interface, and BUS interface
Note: The MENU button function is available only on Engine Premium Edition(s) and Vehicle Platinum Edition(s). This button is not used in Engine Basic Edition(s).
-
MENU button is used to control Warning LED on/off. A single press on MENU button will turn on the Warning LED if the Warning LED is off, and vice versa.
-
The "warning LED" will be constant off in Engine Basic Edition(s).
-
If buzzer enabled, a short beep will be heard to reflect a press on MENU button.
In static mode, all* simulated SAE-J1939 signal will be controlled by the control step value, which in turn can be controlled by the UP and DOWN buttons. In dynamic mode, the simulator automatically adjust the control step value by itself, this will generate dynamic J1939 signals.
-
Press DOWN button:
-
DOWN button is used to decrease the values of all J1939 signal*. Press DOWN button once, all simulated data will decrease one step than the previous data until they reached the minimum values. "DOWN+0%" LED will be triggered on/off.
-
If DOWN+0% LED is on, press DOWN button one time, DOWN+0% LED will be off.
-
If DOWN+0% LED is off, press DOWN button one time, DOWN+0% LED will be on.
-
80% LED blinks when control step value equal to 80%,
-
60% LED blinks when control step value equal to 60%,
-
40% LED blinks when control step value equal to 40%,
-
20% LED blinks when control step value equal to 20%,
-
DOWN + 0% LED blinks when control step equal to 0%,
-
If buzzer is enabled, a short beep will be heard to reflect a press on DOWN button.
-
Press UP button:
- UP button is used to increase the values of all J1939 signal*. Press UP button once, all simulated data will increase one step to next data level until they reached the maximum values, "UP+100%" LED will be triggered on or off.
- If UP+100% LED is on, press UP button one time, UP+100% LED will be off.
- If UP+100% LED is off, press UP button one time, UP+100% LED will be on.
- 20% LED blinks when control step value equal to 20%,
- 40% LED blinks when control step value equal to 40%,
- 60% LED blinks when control step value equal to 60%,
- 80% LED blinks when control step value equal to 80%,
- UP+100% LED blinks when control step value equal to highest value, 100%.
- If buzzer enabled, a short beep will be heard to reflect a press on UP button.
Note: * The Engine Clock is not controlled by the control step value and push buttons; it runs all by itself just like a real clock.
The push button functions are summarized in table 1.
Table 1 Summary of Push button functions
Push Button Operation |
Function |
Press DOWN button |
Decrease all simulated data until it reaches the lowest value |
Press UP button |
Increase all simulated data until it reaches the highest value |
Press MENU button |
DM1 Warning On/Off control (N.A. for Engine Basic Edition(s)) |
Press and hold MENU button when power on |
Simulator will enter Bootloader mode, if no communication is detected from a PC Bootloader program within 10 seconds, it will resume normal mode |
Press and hold both DOWN + UP button |
Buzzer ON/OFF control |
Press and hold both MENU + UP button |
Switch between Static/dynamic mode |
Press and hold both MENU + DOWN button |
Engine DM2 ON/Reset control (N.A. in Engine Basic Edition) |
AU J1939 SIMULATOR REMOTE TERMINAL
All Au J1939 Simulator editions can be easily integrated into a SAE-J1939 network (with a 4-wire cable). And all PLUS editions can be connected to a PC (with a RS232extension cable), as shown in figure 4.
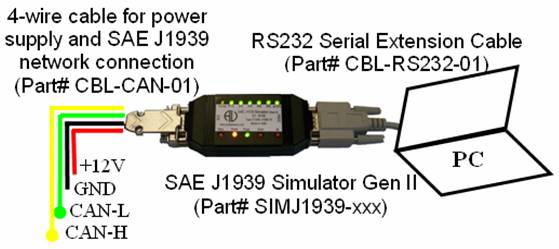
Figure 4 – Typical PC and network Connection of Au SAE-J1939 Simulator
The 4-wire cable (which has a DB9 connector on one end, a pigtail on the other end, can be ordered seperately with Au Part # CBL-CAN-01) for power supply and SAE-J1939 network connection is color coded as shown in table 2.
Table 2 - Color code of 4-wire cable
Color |
Signal |
Red: |
+12 V power supply |
White: |
CAN-H |
Green: |
CAN-L |
Black: |
Ground |
Au J1939 Simulator Remote Terminal is available for all Au J1939 Simulator PLUS editions. It is designed for displaying detail information on all simulated SAE-J1939 signal. The interface includes a control panel and a display panel. The control panel is located in the up-left corner. all the other area display info like engine/ABS/Transmission info, warning lamp, etc. as shown in figure 5 - 1, 5 - 2, 5 - 3.
Figure 5 -1 shows the J1939 Simulator Remote Terminal GUI (Graphic User Interface) for vehicle platinum plus edition. All features are active.
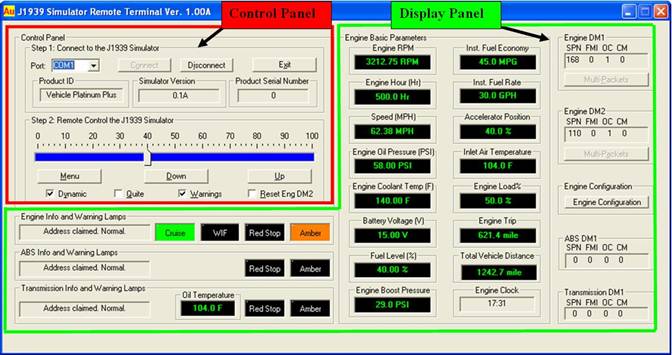
Figure 5 - 1 - Au J1939 Simulator Remote Terminal GUI – Vehicle Platinum Plus
Figure 5 -2 shows the J1939 Simulator Remote Terminal GUI for Engine Premium Plus edition. Engine info and warning lamps, engine basic parameters, engine DM1, and engine DM2 are available. ABS info, Transmission info and engine configuration are not available.
Figure 5 - 2 - Au J1939 Simulator Remote Terminal GUI – Engine Premium Plus
Figure 5 -3 shows the J1939 Simulator Remote Terminal GUI for Engine Basic Plus edition. Engine info and Cruise lamps, engine basic parameters are active for this edition.
ABS info, Transmission info, engine DM1, engine DM2, and engine configuration are not available.
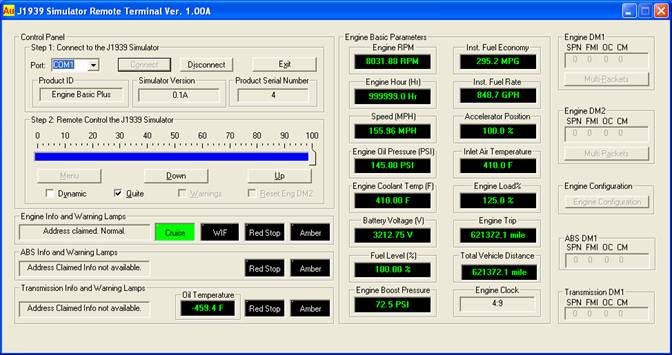
Figure 5 - 3 - Au J1939 Simulator Remote Terminal GUI – Engine Basic Plus
- Display Panel – Engine Basic Parameters
Display the following 16 engine basic parameters: Engine Speed(RPM), Engine hour (Hr), Vehicle speed (MPH), Engine oil pressure (PSI), Engine coolant temperature (F), Battery voltage (V), Fuel level (%), Engine boost pressure (PSI), instant fuel economy (MPG), instant fuel rate (GPH), accelerator position (%), inlet air temperature (F), engine load percentage (%), engine trip (mile), total vehicle distance (mile), and engine clock (HH:MM) (figure 6).
Note: Engine Clock is not controlled by the control step value, it runs by itself like a real clock, and can be setup by PGN 54528.
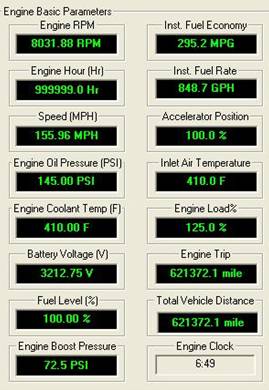
Figure 6- Display panel – Engine basic parameters
- Display Panel – Engine DM1
Engine DM1 message could be one packet (without warning or with 1 warning) or multi-packet.
If engine DM1is a single packet, SPN, FMI, OC, CM will display (figure 7-1). If engine DM1 is a multi-packet, "see @ Multi-Packets" will display, “Multi-packets” button will be active (figure 7 – 2), click on it, the whole list of engine DM1 will display. If Engine DM1 or DM2 warning is off, a SAE defined non-warning message will be shown as (0,0,0,0).
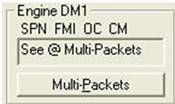
Figure 7 -1- Engine DM1 Single Packet Figure 7 - 2 - Engine DM1 Multi-Packet
- Display Panel – Engine DM2
Engine DM2 message could be one packet or multi-packet. If engine DM2 is a single packet, SPN, FMI, OC, CM will display (figure 8-1). If engine DM2 is a multi-packet, "see @ Multi-Packets" will display, “Multi-packets” button will be active (figure 8–2), click on it, the whole list of engine DM2 will display.
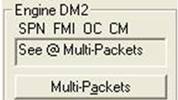
Figure 8 -1- Engine DM2 Single Packet Figure 8 - 2 - Engine DM2 Multi-Packet
- Display Panel – Engine Configuration
Engine Configuration PGN includes 34 bytes of messages which require transport protocol for multi-packet communication. “Engine Configuration” button will be active on the GUI (Figure 9 -1) for vehicle platinum edition(s).
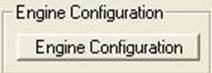
Figure 9 -1 - Display panel – Engine Configuration
ABS DM1 is a single-packet PGN. If ABS warning is off, a SAE defined non-warning message will be shown as (0,0,0,0); If ABS warning is on, a Brake Switch signal low warning will be shown (597,1,7,0) (figure 10).
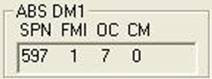
Figure 10- Display panel – ABS DM1
- Display Panel – Transmission DM1
Transmission DM1 is a single-packet PGN. If transmission warning is off, a SAE defined non-warning message will be shown as (0, 0, 0, 0); if the warning is on, a transmission oil warning will be shown as (177, 0, 126, 0) (figure 11).
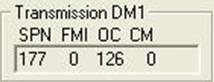
Figure 11- Display panel – Transmission DM1
As defined by SAE-J1939/21, the Au SAE-J1939 simulator response to different “engine DM2 request” with different transport protocols (illustrated in Table 3).
Table 3 – Transport Protocol for DM2 global/specific request
Request |
Transport Protocol |
Global request |
TP.CM.BAM |
TP.DT |
Specific request |
TP.CM.RTS |
TP.CM.CTS |
TP.DT |
TP.CM.EndOfMsgACK |
TP.CM.Abort |